Graphene Foam: Uniaxial Tension Behavior and Fracture Mode Based on a Mesoscopic Model
2017年09月07日
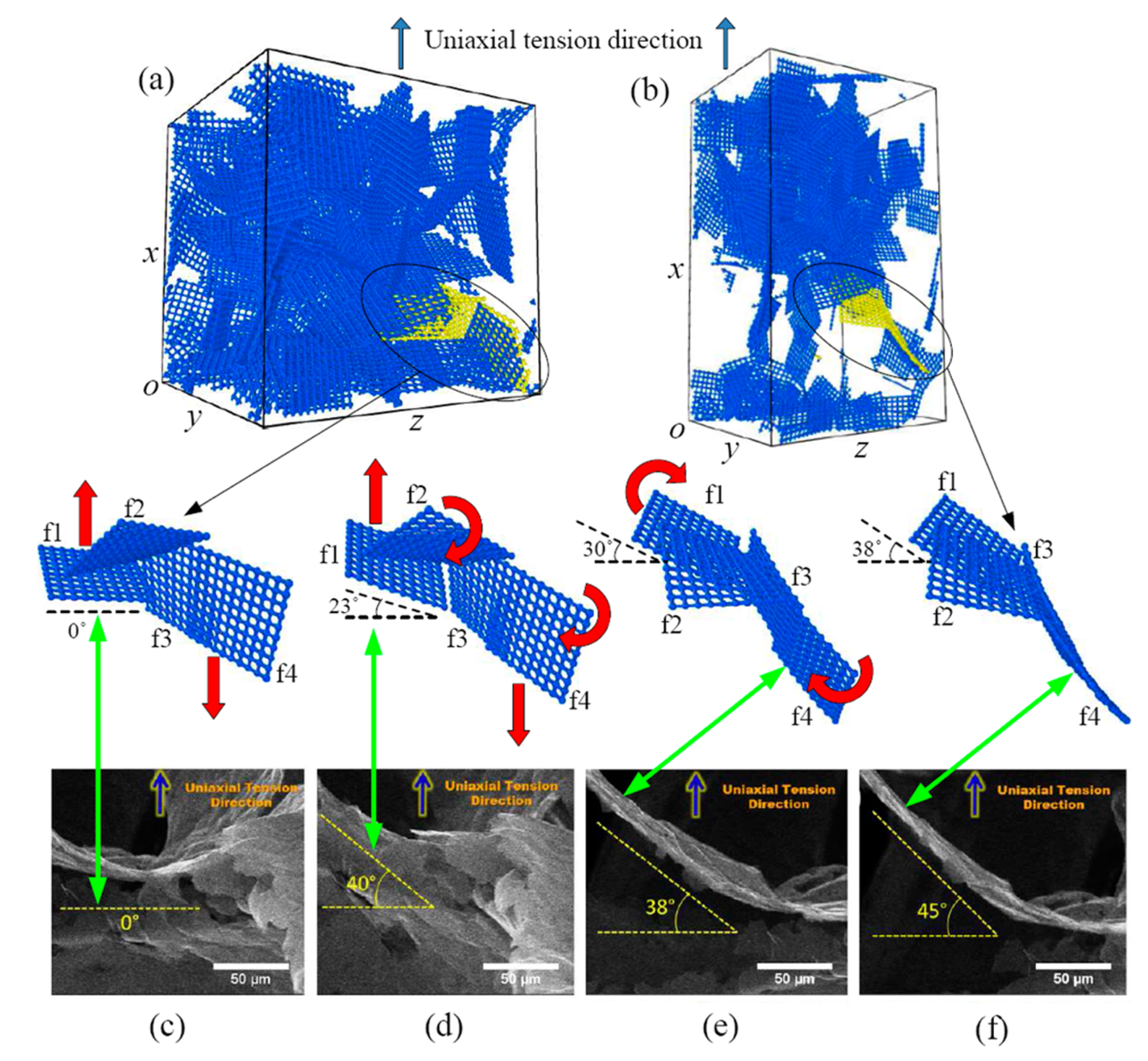
Figure Evolution of mesostructure in tensile deformation. (a) Initial state and (b) final state of the GrF in uniaxial tension, where the local flakes considered are in yellow color. (c–f) Local mesostructures of four sequential thermodynamic states in the tensile deformation (see also Movie S2 in the Supporting Information for the dynamic process) and the corresponding SEM micrographs reproduced from Nieto et al.,(17) where f1–f4 indicate four constituent graphene flakes.
Because of the combined advantages of both porous materials and two-dimensional (2D) graphene sheets, superior mechanical properties of three-dimensional (3D) graphene foams have received much attention from material scientists and energy engineers. Here, a 2D mesoscopic graphene model (Modell. Simul. Mater. Sci. Eng. 2011, 19, 054003), was expanded into a 3D bonded graphene foam system by utilizing physical cross-links and van der Waals forces acting among different mesoscopic graphene flakes by considering the debonding behavior, to evaluate the uniaxial tension behavior and fracture mode based on in situ SEM tensile testing (Carbon 2015, 85, 299). We reasonably reproduced a multipeak stress–strain relationship including its obvious yielding plateau and a ductile fracture mode near 45° plane from the tensile direction including the corresponding fracture morphology. Then, a power scaling law of tensile elastic modulus with mass density and an anisotropic strain-dependent Poisson’s ratio were both deduced. The mesoscopic physical mechanism of tensile deformation was clearly revealed through the local stress state and evolution of mesostructure. The fracture feature of bonded graphene foam and its thermodynamic state were directly navigated to the tearing pattern of mesoscopic graphene flakes. This study provides an effective way to understand the mesoscopic physical nature of 3D graphene foams, and hence it may contribute to the multiscale computations of micro/meso/macromechanical performances and optimal design of advanced graphene-foam-based materials.